To start learning now about how Cash Recyclers can improve your business operations, check out our free infographic here.
3 min read
How Much does a Cash Recycler Cost? Pricing, Freight, & Maintenance
Sean Farrell
:
Dec 10, 2014 8:00:00 AM
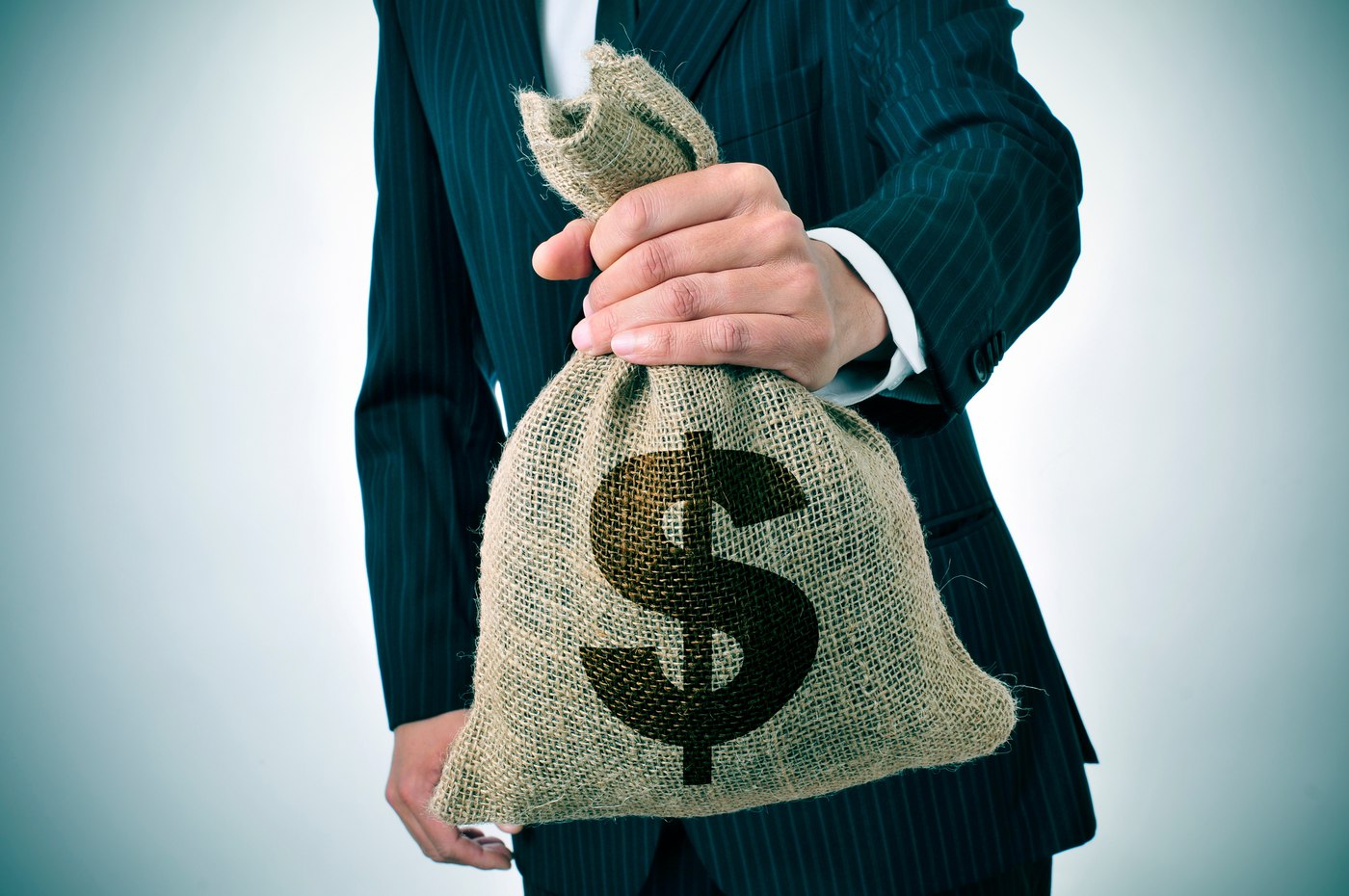
There are several components to understanding the costs associated with purchasing a cash recycler. If you are still unclear on the benefits of the cash recycler I recommend you read the following articles to bring you up to speed on why this technology is so valuable:
- Cash Recyclers: The Best Investment to Improve Branch Operations
- 3 Reasons Financial Institutions Need to Automate their Teller Lines
- How Does a Cash Recycler Help My Teller Line Operate Better
- Carolina Collegiate FCU Sees Immediate Operational Improvements with Cash Recycler
- Jetstream FCU Differentiates Branch Experience with New Design and Technology
Cash Recycler Costs
The 4 main purchasing elements for a cash recycler are:
- The equipment
- Integration
- Freight, installation and training
- Maintenance services
Cost of Cash Recycler Equipment
This is the area most people think about when making a capital expenditure to buy a cash recycler. You have probably researched which model makes sense for you and perhaps even talked to peer institutions about their satisfaction with what they've done.
If you want additional points to consider when purchasing a recycler, we wrote an article that explores the 3 things to consider when buying a teller cash recycler.
Cash recyclers range from roughly $20,000-$36,000 here at QDS. I would say the median price for cash recyclers in the market today is roughly $36,000. There are models sold in the low $40,000s as well as less expensive models starting below $36,000. Another key component to the equipment is whether or not to purchase a coin dispenser.
In my opinion, if you are going to automate the cash side, I would spend the extra $1,500-$2,000 and purchase a coin dispenser with the recycler to automate withdrawals to the penny.
Cost of Cash Recycler Integration
There is another decision to be made here. There are 2 primary ways recyclers are integrated to teller software applications, Middleware and Direct Integration. We covered this topic and the merits of each during this podcast.
Most middleware packages run between $2,000-$3,000 per unit as a ballpark range. This is the upfront cost paid only once. Middleware allows you to integrate a wider array of hardware than perhaps what your teller system can directly support. Direct Integration has a variety of pricing models.
Some teller systems charge a module fee to turn on the integration of $25,000-$50,000. There is also an annual cost of using that module as well. Others price per "seat" or "device", and that pricing may range from $1,000-$5,000 per year per device.
So if you are looking at lower numbers of units needed, the cost of going direct can make the expense tough to swallow. If you are looking at a larger deployment, the scale of the number of units can make direct integration more attractive.
Cost of Cash Recycler Freight, Installation and Training
This area is more important than you may think. If you are undergoing a change in process and have decided to make an investment in cash recyclers, you want to ensure your staff are as comfortable as possible, as quick as possible, and know what to do in the event of a failure or mistake.
The average cost for this is $1,500-$2,500. Most companies use a professional rigger to set the recycler in place (most of the units weigh close to 1000 lbs or more). Freight is another important aspect since most of the units come from overseas and that cost is typically passed through to the customer very similarly to a car.
Lastly is that training piece. Some companies bill for this separately and some include it in the bundle of this category. Here at QDS we bundle this number all into one number per unit so you have a clear understanding of all your costs.
Cost of Cash Recycler Maintenance Services
Most cash recyclers are great machines and will run well if you treat them well. However, maintenance is usually a necessary relationship that you can't go without.
Parts cost on most recyclers is high, which is what tends to drive the cost of the service agreement up. A good rule of thumb is 10% of the equipment price is a normal expectation for service maintenance price.
For example, if you paid $35,000 for the recycler, $3,500 is a normal number to expect for annual maintenance including preventative maintenance, parts, labor and travel all included. Some may charge less, some more, but you at least know a good number that's a fair price in the market.
Just about everyone offers either billable as needed service or contract service. Most companies will also have a 4-8 hour response time on cash recyclers due to their mission critical nature in the branch.
Final Thoughts
There are multiple components to any cash automation purchase and hopefully you found this article helpful in defining general pricing. Typically the more you buy the lower the costs can be.
Most cash recyclers carry an ROI of 18-24 months, but it varies by location and staffing decisions. If you need help determining what your ROI would be, fill out our contact form and we'd be happy to see if a recycler is a fit to address your needs.
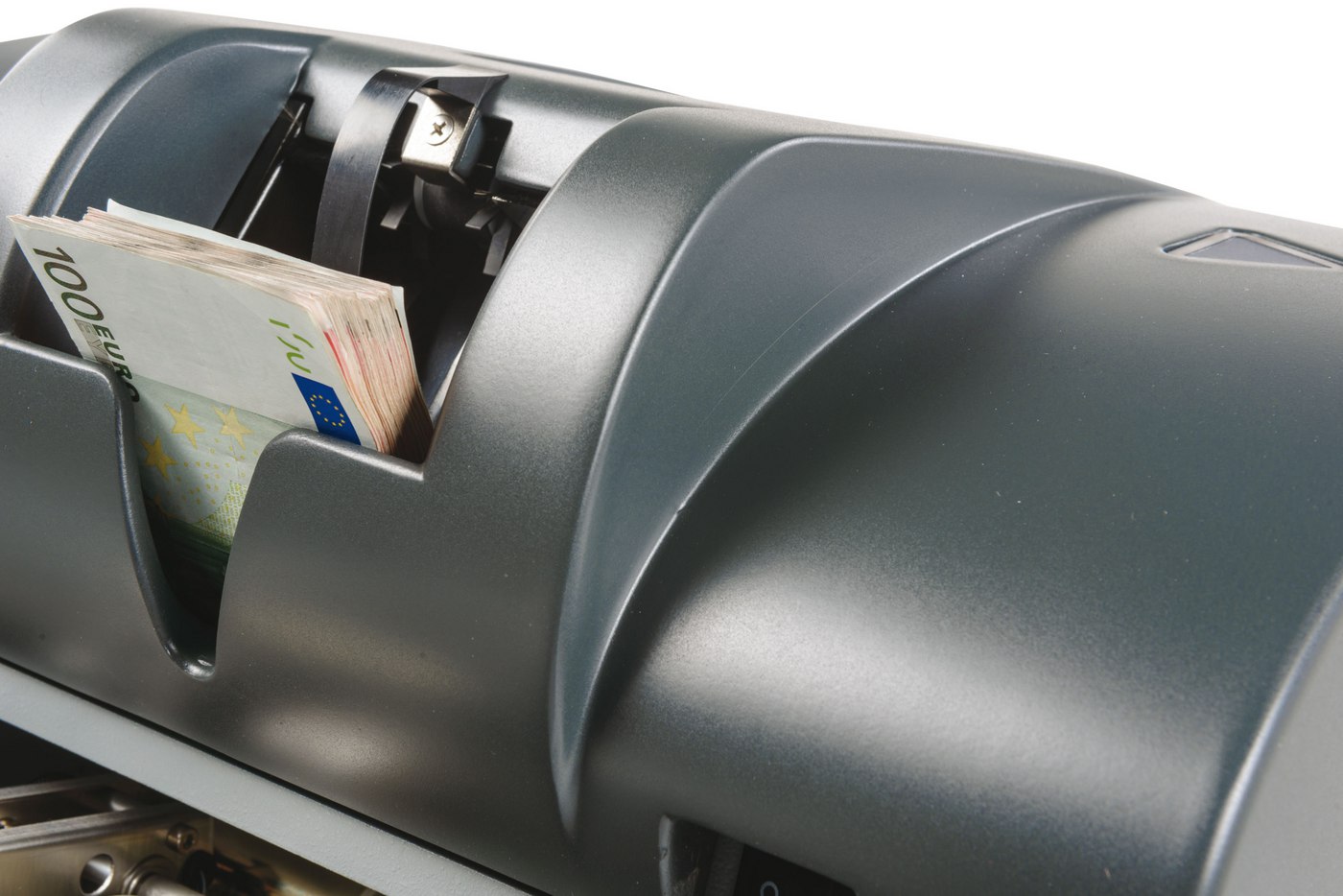
How Does a Cash Recycler Work?

A cash recycler is an amazing wonder of technology, even to those of us in the business. I am reminded when I am on-site for installs, when those...
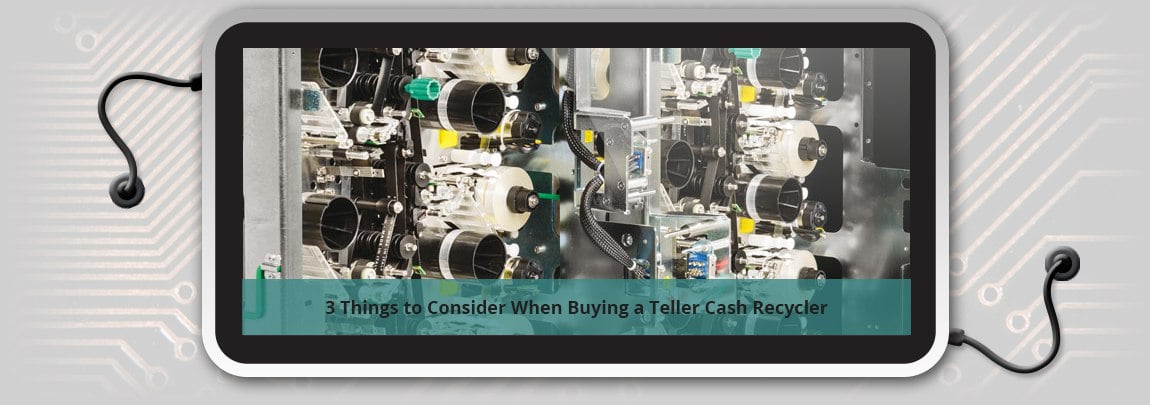
3 Things to Consider When Buying a Teller Cash Recycler

You have researched the market for what you can do to make your branches more efficient and help streamline the customer experience. You’ve read...
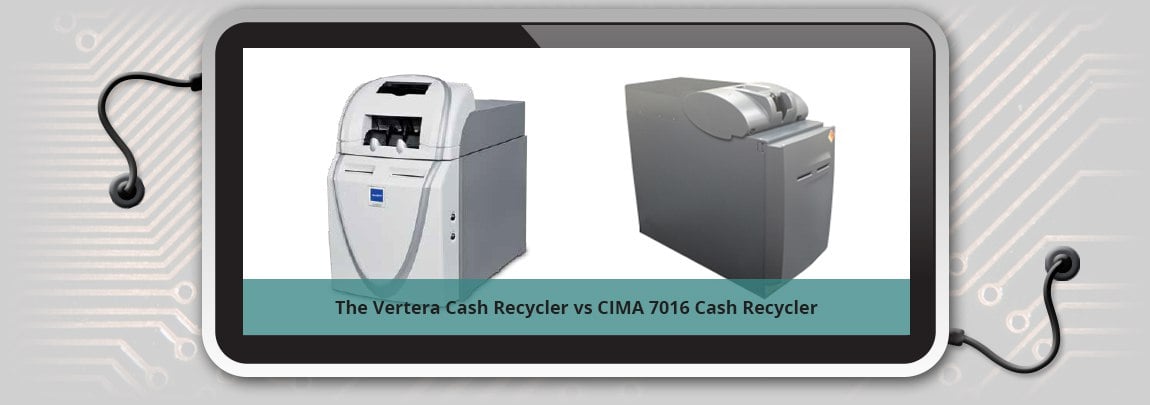
The Vertera Cash Recycler vs CIMA 7016 Cash Recycler

Why should I automate with a cash recycler? Sure cash recyclers can be big investment for a small to mid-size financial institution. That's exactly...